Is Concrete Leveling Worth It? The Pros & Cons of Concrete Leveling
August 15th, 2022 | 3 min. read
By Sarah Etler
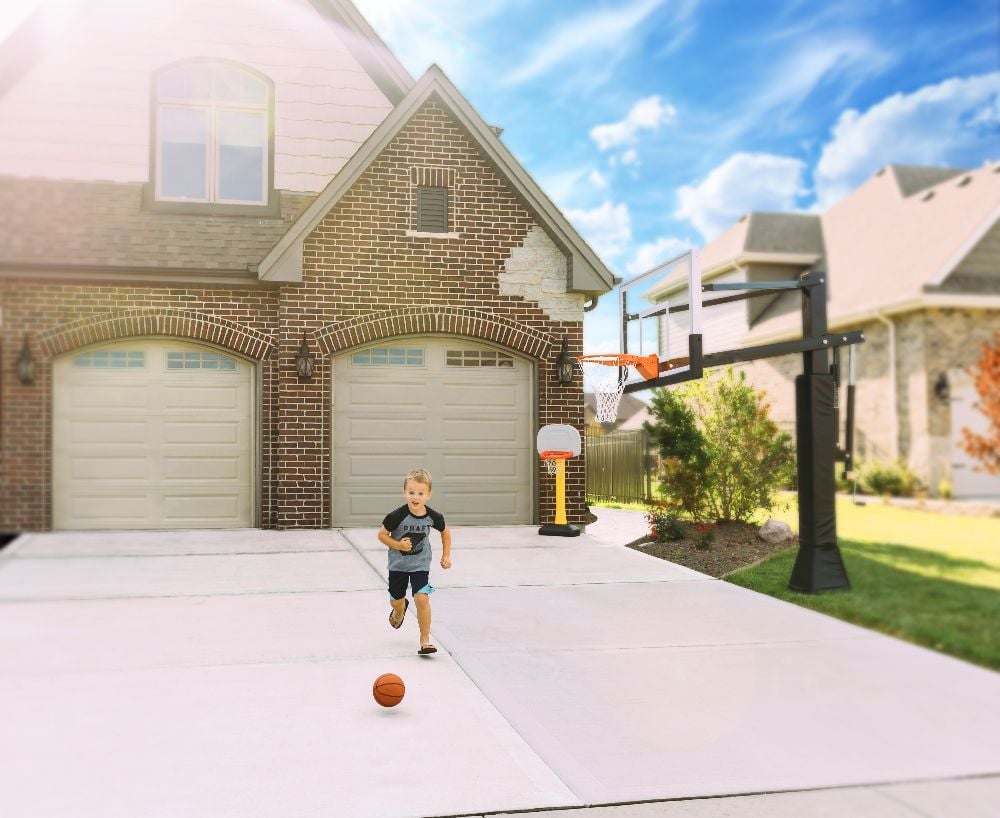
Learn about the good, the bad, and the ugly of concrete leveling, and find out whether its a method worth exploring for your sinking concrete.
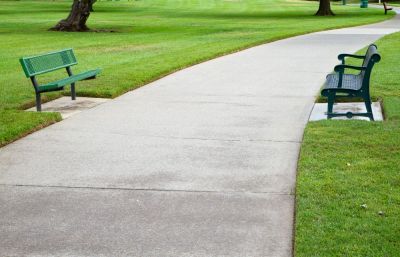
If your property is riddled with trip hazards and unsightly settled concrete, then having it professionally leveled may be a great option for you. However, concrete leveling is not the only method out there, so it's essential to consider each potential choice carefully before committing to one over the other.
Here at A-1 Concrete Leveling, we've been specializing in our own proprietary limestone slurry concrete leveling process for over 30 years, and we also perform foam leveling repairs when needed.
Although we think concrete leveling is a fantastic option that saves our customers lots of money, we want to be transparent about both the advantages and disadvantages of concrete leveling.
Because of this, we've compiled this list of some of the pros and cons of concrete leveling. After reading, you'll walk away with all the information you need to decide whether professional concrete leveling is something worth exploring for your home.
Concrete Leveling Pros & Cons Overview
The table below shows an overview of the pros & cons of concrete leveling, and the sections that follow discuss them in detail.
Pros | Cons |
---|---|
|
|
|
|
|
|
|
The Pros of Concrete Leveling
Here are the top four advantages of all types of concrete leveling:
-
Extremely cost-effective
One of the most notable benefits of concrete leveling is its price compared to replacement. As long as your concrete slab isn’t crumbling, it can likely be recovered with concrete leveling for far less than it would cost to replace the slab.
On average, concrete leveling can save you up to 70% of the cost of replacement.
-
Quick turnaround time
Most of the time concrete leveling crews are in and out in less than a day. Instead of spending weeks demolishing existing structures, clearing out material, and waiting for your concrete to cure, you can use your freshly-leveled concrete in a matter of hours.
-
Convenience
It’s fairly easy to find a trustworthy and experienced concrete leveling company in your area that can come to give you an estimate and have your work completed quickly and without any hassle, especially if you know how to ask the right questions. A-1 Concrete Leveling has franchises in nearly 50 metropolitan areas!
It’s also much more convenient to have a truck in the driveway once for a short time during the repair, rather than for days or weeks during a replacement.
-
Matching slabs
Other repair methods, like concrete replacement, make it almost impossible to match new materials to the surrounding concrete slabs, leaving you with noticeable differences. Concrete leveling, however, will keep your original slabs the same, so all existing concrete will match.
The Cons of Concrete Leveling
Here are the top three disadvantages of concrete leveling:
-
Breaks don’t go away completely
Because concrete leveling doesn’t actually change the existing concrete, only its position, the cracks and breaks that have already formed will not go away. Sometimes the breaks will get smaller or larger depending on the circumstances of the repair.
Fortunately, these cracks can be filled with a polymer caulk in order to prevent further damage from freeze-thaw cycles and water erosion.
-
Can’t always predict the outcome
While it would be nice to know how every repair will turn out, the truth is that a good concrete leveling job has to take into account a lot of variables, and some of them are unknown until the repair begins.
The good news is that the right concrete leveling company will be experienced and know how to roll with hidden obstacles.
-
Only as good as the ground it's on
Much like concrete replacement, concrete leveling depends on the quality of the material under the slab to ensure a durable repair. If the ground under a leveling job isn’t strong, over time, problems can arise or settling can reoccur.
This is why having a trustworthy and knowledgeable concrete leveling team is important. While no job has a 100% guarantee of perfection, an experienced crew knows what to watch out for.
Summary
Lifting your settled and sunken concrete with professional leveling services can save you lots of money, time, and hassle. With all the benefits listed above, it's clearly a great choice for many homeowners who want to get the job done right.
While this is true, concrete leveling does come with some potential drawbacks, and it's important to keep these in mind while deciding whether or not it's a repair method you would like to try for your home.
Contact A-1 Concrete Leveling
Once you've weighed the pros and cons of concrete leveling and decided it just may be the right fit for you, you're ready to reach out to a concrete leveling specialist.
A-1 Concrete Leveling has been perfecting the art of concrete leveling for over 30 years and is excited to continue providing repair and maintenance services to new and returning customers alike.
If you're ready to get started, click the link below to request a free onsite cost estimate with one of our concrete repair experts today!
Click Here to Find Your Nearest Location and Receive a FREE Estimate
Want to know more?
Check out these related topics from our Concrete Academy:
Sarah Etler joined A-1 Concrete Leveling after receiving her Bachelor of Arts degree in English from Northern Kentucky University. As A-1's Content Marketing Manager, she works closely with industry experts to produce content that will best answer questions related to concrete repair and maintenance practices. Sarah loves living a life full of discovery and is excited every day to see what new things she can learn and share with those around her.
Topics: